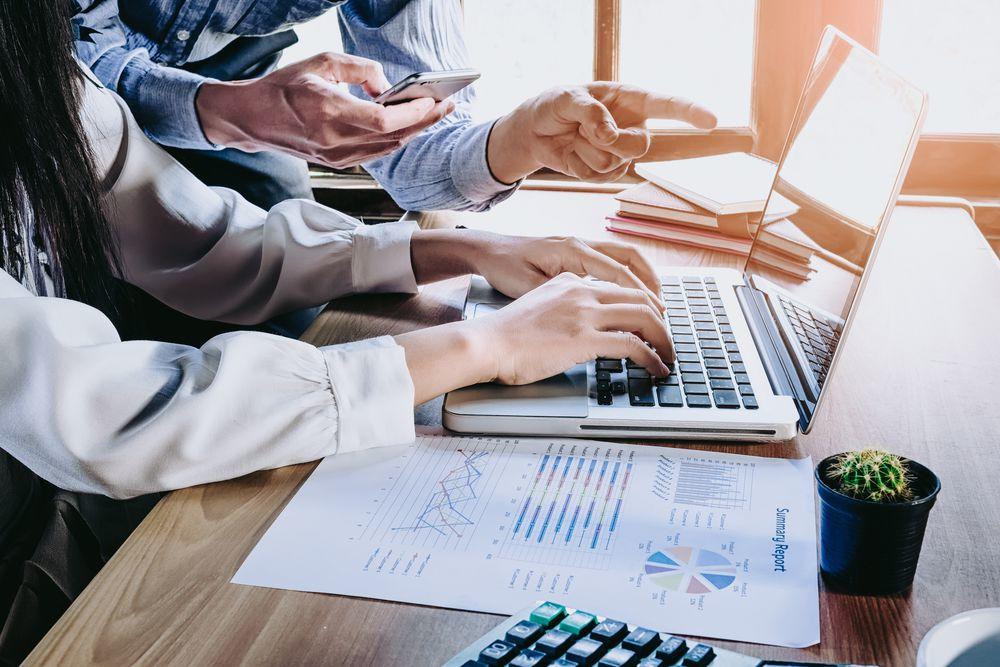
Guia completo para entender a metodologia lean de uma vez por todas
A metodologia lean já existe há algum tempo. Desde que seus princípios foram definidos, no início do século 20, a montadora de veículos Toyota fez algumas modificações para ajustá-la às suas necessidades e criar um sistema mais adequado à produção no final dos anos 80.
Naquela época, a metodologia era chamada de Toyota Production System, mas, atualmente, o termo lean tem sido mais amplamente aceito — por ser generalista e neutro, é aceito como padrão pela indústria da transformação.
Em anos recentes, o lean ganhou importância e relevância no setor de serviços e passou a englobar hospitais, bancos e, principalmente, empresas no ramo da Tecnologia da Informação (TI). Ainda não conhece a metodologia? Então continue a leitura deste artigo e aprenda tudo sobre ela!
O que é metodologia lean?
O termo lean (do inglês, enxuto) foi escolhido para descrever o método que a Toyota implementou em sua linha de produção no final da década de 1980. A metodologia busca reduzir o desperdício de recursos e, por isso, tudo o que não estiver agregando valor ao produto ou serviço deve ser removido do processo — pois representa um custo que pode ser evitado, como desperdício de tempo, de materiais, de mão de obra e de outros recursos.
Ou seja, a metodologia lean é dedicada a manter o foco no corte de custos desnecessários e, paralelamente, aumentar o valor agregado ao cliente. E isso é feito implementando um fluxo de processos mais simplificado.
Quando falamos em agregar valor, queremos dizer produzir receitas. Se isso não estiver acontecendo, a companhia vai acumular custo e despesas, indo na contramão do ideal. Parece fácil na teoria, mas a prática pode ser um pouco mais complicada.
No setor de TI, os princípios do lean são aplicados ao desenvolvimento de software, ao gerenciamento de aplicações, ao suporte e à prestação de outros serviços relacionados à TI. O principal objetivo é eliminar tarefas e funcionalidades que não agregam valor e potencializar o que for comprovadamente mais lucrativo.
Embora a metodologia seja bem estabelecida e tenha ampla aplicabilidade, no ramo da TI seu uso ainda é tímido. Porém, à medida que seus benefícios vão sendo descobertos, mais gestores passam a adotá-la.
Provavelmente, o lean é a abordagem mais intuitiva que se pode utilizar para alcançar a melhoria nos processos, pois o foco é direcionado para o público com simplicidade, fluxo contínuo, visibilidade e boas parcerias. Como resultado, deve aumentar o valor percebido pelo cliente, impulsionando o aumento das vendas e a margem de lucro.
Como funciona a metodologia lean?
Se a ideia principal é criar o máximo de valor com o mínimo de recursos possível, a empresa deve compreender bem o que é importante para o cliente e concentrar seus esforços em satisfazê-lo de forma adequada e contínua. No final, ela precisa entregar um produto ou serviço que supere as expectativas, proporcionando valor com desperdício zero.
Para conseguir isso, as organizações precisam mudar o foco do gerenciamento de tecnologias, processos, ativos e departamentos somente no sentido vertical para adotar também o fluxo horizontal, criando valores em todas as direções e de maneira integrada em todas as etapas.
Todos os departamentos são interdependentes e a melhor integração ajuda a criar um produto ou serviço mais completo e com melhor valor agregado — reduzindo desperdícios no processo.
Quando essa integração acontece, pode-se criar um padrão com processos que precisam de menos esforço humano, menos espaço físico, menos capital investido e menos tempo para produzir produtos e serviços. Com isso, menos custos e defeitos ou falhas são registrados em comparação com sistemas produtivos tradicionais.
Ao adotar o lean, a empresa torna-se capaz de responder mais rapidamente às mudanças no cenário econômico, nas demandas e nos perfis de clientes, mantendo a qualidade, com custos e tempo de produção reduzidos. Além disso, o gerenciamento de informações torna-se muito mais simples e preciso.
O método envolve o pensamento crítico na análise e na definição de uma operação totalmente livre de desperdícios e capaz de maximizar o valor agregado. Dessa forma, a transformação ocorre quando a empresa alcança um nível de aprimoramento contínuo em todos os processos, criando um ambiente de profundo envolvimento e estimulando a cooperação entre os envolvidos.
Como a metodologia lean é vista no ramo de TI?
Um equívoco comum é achar que lean é adequada apenas para empresas que têm uma linha de produção física. Na verdade, ela se aplica a todos os tipos de negócios e processos. Não se trata de um simples programa de redução de custos, mas de uma maneira de pensar na empresa como um todo, ajustando e integrando cada atividade para otimizá-la.
Hoje, gestores de todos os segmentos estão usando os princípios básicos de lean e mudando a forma como pensam e agem. É claro que muitos preferem usar outros nomes para rotular a estratégia como se ela fosse exclusiva da empresa. O fato, porém, é que a metodologia é a mesma, com poucas alterações.
A necessidade de estabelecer um sistema de produção enxuto para manter a competitividade é grande e acontece em todos os segmentos da economia atualmente. Isso tem levado muitas empresas a adotarem lean, inclusive, as do segmento de TI. Profissionais do setor identificaram muitas similaridades entre as atividades de uma empresa de TI e uma de fabricação de autopeças, por exemplo.
A principal diferença é que, enquanto uma fábrica produz bens de valor agregado, empresas de TI entregam serviços e produtos digitais com valor agregado. Semelhantemente a uma fábrica de peças, a empresa de TI também precisa gerenciar recursos, demanda, controle de qualidade, segurança e assim por diante.
Quais os benefícios do lean aplicado à gestão da empresa?
Os clientes estão ficando cada vez mais exigentes e, como resposta, os produtos e serviços mais personalizados. E mais: o ciclo de vida deles é encurtado ao ponto de produzir renda recorrente para as empresas. Esse cenário é o que tem impulsionado o uso do lean.
À medida que uma empresa se desenvolve, os processos crescem junto para atender a demanda. O problema é que, muitas vezes, isso resulta no surgimento de técnicas ineficientes e/ou desnecessárias.
É aí que entra a lean. A metodologia desafia a maneira como as coisas são feitas e abre os olhos dos gestores para o desperdício de recursos e as eventuais ineficiências que estejam criando gargalos na produção.
A lean deve melhorar a produtividade, agregar mais qualidade a ela, contribuir para a redução dos prazos de entrega e liberar mais recursos para suportar o crescimento da empresa. Como consequência, ela ajuda a aumentar o poder competitivo no mercado.
Quando a empresa implementa a metodologia, passa a liberar mais espaço físico em toda a fábrica. Assim, pode adicionar novas linhas de produtos e serviços ao portfólio, reduzir a necessidade de terceirização e aumentar a produção das linhas existentes com qualidade e sem a necessidade de adquirir novas instalações, equipamentos e mão de obra.
Isso dá à organização uma clara vantagem competitiva em relação a outras empresas do mesmo segmento. De forma resumida, listamos os principais benefícios da metodologia lean. Acompanhe.
As etapas da produção ganham sincronia
A metodologia lean permite enxergar com mais clareza os diferentes indicadores de um negócio em cada uma de suas etapas. Os administradores japoneses que originalmente a conceberam se inspiraram no funcionamento dos supermercados.
Em um supermercado, os clientes retiram os produtos apenas no momento em que precisam: nem antes, nem depois. O fluxo dos estoques responde com precisão e rapidez às demandas de cada momento. Foi esse tipo de modelo que a Toyota passou a ter em mente para evitar que uma parte da montagem do veículo tivesse de ser interrompida porque a peça não chegou a tempo, por exemplo.
A produção ganha qualidade
Em um ambiente de trabalho enxuto, qualquer defeito ou atraso aparece com facilidade. Isso não vai impedir os erros, mas permite que eles sejam identificados e corrigidos rapidamente. Com procedimentos padronizados, os funcionários vão se especializando em uma rotina e os bons resultados aparecem como que por memória muscular.
A maioria das falhas é eliminada
A metodologia lean envolve tanto a criação de um ambiente no qual os erros sejam identificados facilmente quanto corrigidos com rapidez. Qualquer anomalia se destaca mais se o ambiente não tem bagunça e os prazos, ritmos e procedimentos são rígidos. Além disso, os próprios funcionários são estimulados a encontrar e corrigir falhas sem precisarem de instruções específicas para isso.
Os custos operacionais são diminuídos
Adotar a metodologia lean significa livrar a empresa de custos com excesso de estoque, reduzir atrasos e colocá-la em posição mais vantajosa para negociar com clientes e fornecedores, ao ter melhor informação sobre os custos operacionais. Até mesmo custos com conta de luz e combustível podem ser reduzidos com essas técnicas.
O ciclo de produção é reduzido
Assim como aconteceu com os engenheiros da Toyota, o ciclo de produção da sua empresa pode ser reduzido, permitindo a ela entregar mais produtos e serviços no mesmo tempo. Isso acontece porque os gargalos serão identificados e corrigidos, e como consequência das diferentes etapas passarem a andar em ritmo mais parecido.
A produtividade é melhorada
Seus funcionários vão passar a dominar mais o próprio trabalho pela adoção de procedimentos padronizados e, com isso, sua produção aumentará, pois eles estarão mais satisfeitos. Gargalos ou atrasos dentro ou entre cada procedimento também serão corrigidos, melhorando o sentimento de trabalho em equipe.
As receitas aumentam
As receitas de sua empresa vão aumentar com os ganhos de produtividade. Além disso, custos com materiais e procedimentos desnecessários serão cortados, resultando em um reforço ainda maior para o caixa da sua empresa.
Quais princípios e ferramentas que formam a metodologia lean?
Para que a lean seja colocada em prática com eficiência, será necessário contar com ferramentas e outras técnicas que, juntas, complementam a sua estratégia. Confira quais são elas.
5S (organização do local de trabalho)
É uma ferramenta simples, mas muito eficiente, que ajuda a organizar o local de trabalho, deixando-o mais limpo, funcional e seguro. O 5S contribui para melhorar a produtividade, aumentar a visibilidade das tarefas e garantir um fluxo de trabalho mais padronizado.
Assim como a metodologia lean, as técnicas da 5S foram concebidas por executivos japoneses e podem ser aplicadas em qualquer lugar de trabalho. Os 5 “S” em inglês são:
- Sort (separar): identificar e classificar os objetos na mesa de trabalho ou na linha de montagem e remover tudo o que for desnecessário. Isso inclui revistas e jornais velhos, blocos de anotações já usados etc. Também pode ser aplicado aos arquivos digitais obsoletos, liberando espaço em disco nos equipamentos da empresa;
- Set in order (ordenar): posicionar os objetos necessários ao trabalho nos locais corretos, onde serão mais úteis. Esse procedimento também aumenta a segurança no local de trabalho, ao garantir que os itens de segurança (sejam eles capacetes ou a chave da sala do servidor) estarão sempre no mesmo lugar;
- Shine (fazer brilhar): manter o ambiente limpo e organizado. As ferramentas de trabalho devem ter sempre o aspecto de novo ou quase novo. Isso faz a empresa ganhar muito tempo e eficiência porque qualquer desvio da norma (um equipamento sujo, com bateria fraca etc.) será detectado e corrigido rapidamente;
- Standardize (padronizar): criar e manter padrões para todos os processos. Cada tarefa na empresa, desde fazer um pedido de compra a entregar um produto para o cliente, deve seguir um processo pré-definido e que esteja disponível para consulta dos funcionários. Em outro jargão é o que chamamos de “SOP” (standard operating procedure, procedimento operacional padrão);
- Sustain (sustentar): estabelecer uma cultura na qual os funcionários façam a coisa certa sem precisar de ordens diretas (inclusive, manter o ambiente de trabalho limpo e organizado, e seguir padrões). Também inclui manter um elevado nível de disciplina na empresa e fazer inspeções regulares para detectar erros e problemas para corrigi-los o quanto antes.
Mapeamento de processos e de fluxo de valor
O diagrama de espaguete e o mapa de fluxo de valor são algumas maneiras poderosas de identificar e destacar o que está sendo desperdiçado nos processos produtivos. Essas ferramentas permitem a criação de mapas para identificar o que gera valor aos clientes e, também, possibilitam a elaboração de planos de ação com foco na melhoria do trabalho.
Em TI, o fluxo de valor é representado pela função exercida internamente em favor da empresa e pelos serviços prestados aos clientes, fornecedores, investidores, reguladores do setor, mídia e outras partes interessadas.
Produção Just in Time (JIT) e Kanban
A JIT é um dos principais pilares da metodologia lean, pois considera a entrega do que o cliente quer, quando quer, onde quer e nas quantidades que quer. Essa estratégia promove uma redução considerável de estoques e melhora o equilíbrio no fluxo de processos.
Para isso, é preciso usar as técnicas Single Minute Exchange of Die (troca rápida de ferramentas) para reduzir o tempo de setups (configurações) e o tamanho de lotes necessários na produção. Além disso, é importante implementar o Kanban para construir um fluxo de processos claro, que possa guiá-lo com o objetivo de eliminar as tarefas menos necessárias.
Kaizen
O Kaizen se concentra em aprimorar cada processo da empresa individualmente. Organizado por eventos, é criado sempre que algo precisa ser melhorado. Assim que o objetivo é atingido, sua função é encerrada. Esse método pode ser utilizado de modo contínuo e vai depender das necessidades de mudança em cada setor da empresa.
Jidoka e Poka Yoke (sistemas à prova de erros)
Outro pilar importante da metodologia lean, o Jidoka foi um dos métodos que apoiou o sistema de produção da Toyota. Ele é focado em qualidade e abrange ideias como a automação, que está dando às máquinas o toque humano para que interrompam o processo sempre que algo sair do comum.
O Poka Yoke (teste de erro), por outro lado, evita que as falhas continuem sendo produzidas, aceitas e/ou retransmitidas após a descoberta para não se tornarem parte do processo. Juntos, o Jidoka e o Poka Yoke formam um alto padrão de qualidade para os produtos e serviços.
Manutenção Produtiva Total
O Total Productive Maintenance (TPM, Manutenção Produtiva Total) equivale à Gestão de Qualidade Total (Total Quality Management — TQM) e envolve todos na organização para a eliminação de seis dos principais desperdícios identificados — e que são monitorados pela métrica Overall Equipment Effectiveness (OEE).
O TPM baseia-se em programas de manutenção preventiva e preditiva, envolvendo a manutenção autônoma das máquinas. Essa é outra pedra angular da metodologia lean, já que garante não só processos mais confiáveis, como também estabelece padronização, resultando em uma qualidade superior do produto ou serviço acabado.
Demais métodos e ferramentas
A metodologia envolve, ainda, uma extensa lista de ferramentas e outros métodos que se complementam. Poderíamos ficar o dia todo discutindo sobre cada uma, mas apresentamos a seguir as que ainda não foram mencionadas neste guia — o que não significa que sejam menos importantes. São elas:
- Análise Modal de Falhas e seus Efeitos (Failure Mode and Effect Analysis — FMEA);
- TOPS/8D (Team Oriented Problem Solution/8 Disciplines);
- Padronização ou Trabalho Uniformizado;
- Heijunka ou Programação Nivelada;
- Gestão a Vista e Controle Visual;
- The 5 Whys (Os cinco porquês);
- Fluxo Contínuo de Informações;
- Sincronização com o Takt Time;
- Diagrama de Causa-Efeito;
- Trabalho em Células;
- Sistema Pull.
Como aplicar a metodologia lean no seu negócio?
Comece descobrindo o que gera valor para o consumidor
Identificar o que gera valor e eliminar todas as outras atividades desnecessárias é a abordagem que deve ter sempre em mente. Então, comece avaliando as regras, as normas e os procedimentos executados em todos os setores da organização.
Quando você descobre que apenas uma fração do tempo e dos processos realmente adicionam valor para o cliente final, ganha uma base para definir claramente o que deve ser reforçado e o que deve ser abandonado.
Identifique os sete maiores desperdícios de TI
Em um ambiente de fabricação, os sete principais geradores de desperdícios são:
- fluxo de processos: você deve pensar sobre como as tarefas passam de um profissional para outro nos processos de desenvolvimento, design, testes, entrega, manutenção e suporte. Quando você entrega uma determinada tarefa para o próximo responsável, se ele não estiver preparado e aguardando para iniciá-la de imediato, não conseguirá criar fluidez na produção;
- acúmulo de tarefas: quanto mais tarefas um profissional aguarda de uma única vez, mais estoque se forma, pois ele não conseguirá lidar com todas as demandas ao mesmo tempo quando chegarem até ele, atrasando o fluxo da produção;
- falta de integração: manter os profissionais trabalhando de forma isolada ou em grupos separados dificulta a comunicação, resultando em desperdícios de tempo;
- tarefas em espera: as tarefas que estão aguardando algo ou alguém adicionam tempo de valor não agregado ao processo e atrasam a entrega não apenas desse item, mas de todos os outros que vêm em seguida, complementando o projeto;
- superprodução: muito tempo costuma ser desperdiçado com o desenvolvimento de recursos que raramente serão utilizados. Satisfazer todas as necessidades do cliente logo de cara não é financeiramente viável e, por isso, será necessário descartar uma série de recursos para tornar o processo mais rápido e objetivo;
- superprocessamento: quando a empresa tem um fluxo de processos muito complexo, ganha tarefas e responsabilidades sobrepostas. A melhor maneira de evitar isso é fazendo um mapa de fluxo de valor para descartar o que não é necessário agora;
- falhas: além das falhas de funcionalidades, se o cliente assinar um plano de algum produto ou serviço e ele não corresponder às suas expectativas, significa que você terá sérios transtornos que podem comprometer a imagem da sua empresa.
Use o quadro Scrum (Kanban)
A maioria dos profissionais de TI ao redor do mundo já incorporou o lean aos processos e usa o quadro Scrum que, na verdade, funciona como um Kanban. Isso não significa que o lean seja um substituto para o Scrum, mas sim, uma metodologia complementar.
Enquanto o Scrum é utilizado para ajudar a controlar um ciclo de desenvolvimento de software, o lean examina todos os processos envolvidos, incluindo muito mais do que apenas um ciclo de desenvolvimento individual. Então, é possível usar o Scrum como ferramenta em qualquer projeto lean.
Configure um sistema pull
Um sistema de empuxo (pull) é utilizado para iniciar a próxima tarefa apenas quando a atual for concluída. Isso significa reduzir a quantidade de trabalho em filas de espera. Esse sistema pode parecer o oposto do quadro Scrum no início, uma vez que defende o comprometimento com um certo número de tarefas a serem entregues em um sprint.
Se você olhar mais a fundo, verá que ao se comprometer com as tarefas, não significa que tenha de adicioná-las ao quadro imediatamente. De fato, reduzir a quantidade de afazeres ajuda a equipe a se concentrar em trabalhos mais específicos e não ficar pulando de uma tarefa para outra sem antes adicionar algum valor como resultado.
Isso é o que chamamos de tempo de configuração, que corresponde a tudo que pode gerar um grande desperdício de tempo. A melhor maneira de definir o tempo de configuração em um ambiente de desenvolvimento de TI é planejar as ações e comportamentos que cada profissional deve ter ao terminar uma tarefa e iniciar outra.
Primeiramente, ele tem de limpar a mente da tarefa anterior para depois começar a outra. A partir daí, deve começar a registrar o tempo de trabalho desempenhado em algum sistema de monitoramento. Além disso, precisa de um período para compreender a nova tarefa, pois ele pode precisar puxar o código em questão do servidor GIT, encontrar o arquivo apropriado e finalmente começar a trabalhar na tarefa.
Todas essas etapas são necessárias para configurar o trabalho e isso pode demorar. Esse é o tempo de configuração.
Agora, imagine se um desenvolvedor precisa fazer isso constantemente sempre que é solicitado em uma nova tarefa. Ele deixa de finalizar as que estão em andamento para iniciar outras, classificadas como mais urgentes. Considerando o tempo de configuração para iniciar cada nova tarefa, muito tempo é desperdiçado durante o dia.
Reduzir o tempo de configuração é uma das medidas mais importantes que devem ser tomadas ao aplicar a metodologia lean em um ambiente de desenvolvimento de TI, pois trará mais benefícios com o mínimo de esforço.
O ideal é que o sistema trabalhe a favor da empresa. Se você não tiver uma forma de monitoramento eficaz ou uma maneira de ter uma visão geral sobre o que foi e o que precisa ser feito, isso funcionará contra você e aumentará o tempo de configuração dos profissionais envolvidos.
Calcule o custo da baixa qualidade
O custo da baixa qualidade (Cost Of Poor Quality — COPQ) é o gasto que deve desaparecer quando todos os processos, sistemas, produtos e serviços funcionarem perfeitamente.
Ele é considerado um custo substancial que a empresa herda de todos os problemas anteriores. Geralmente, é comparado a um iceberg, pois você só enxerga 10% dele (a ponta do iceberg) enquanto os outros 90% ficam implícitos, formando uma grande base de custos consequentes e cumulativos.
No setor de TI, as falhas dos sistemas podem ser consideradas COPQ, ou seja, representam os 10% visíveis, enquanto as causas dessas falhas podem somar os outros 90%. Geralmente, são identificados por sistemas de rastreamento de falhas nos códigos, o que pode levar à descoberta de gerenciamento incorreto, desenvolvedores com baixa qualificação, uso inapropriado da tecnologia, falta de registros, entre outros.
Isso quer dizer que, quando você identificar um problema, deve continuar cavando bem fundo até chegar à origem dele. A famosa frase “cortar o mal pela raiz” descreve bem o que deve ser feito aqui.
Conte com apoio especializado
Implementar a metodologia lean sozinho pode ser trabalhoso e arriscado. A falta de conhecimentos, habilidades e experiências pode levar à implementação de métodos e ferramentas inadequados e que não conversam entre si, gerando um problema ainda maior. Por isso, o ideal é que a empresa tenha o apoio de uma equipe de profissionais especializados no assunto.
Além do suporte em todas as etapas (análise, planejamento, implementação e monitoramento), há uma grande troca de know how entre os profissionais de fora e de dentro da empresa, o que pode servir como um ótimo método de atualização para eles.
A metodologia lean vai ajudar sua equipe a se concentrar no que realmente é importante e, ainda, ajudar a criar valores, reduzindo os índices de distrações e trabalhos desnecessários. Isso significa que o chamado Process Lead Time (PLT) também será reduzido, diminuindo o caminho e o tempo que as tarefas percorrem, desde o pedido até a entrega.
Ficou interessado em saber mais sobre o que a metodologia lean pode fazer para sua empresa? Então deixe um comentário neste post e entre na conversa sobre as vantagens dessa metodologia.